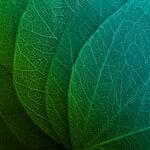
Evolving the Green Chemist’s Toolbox for APIs Manufacturing
Facing a highly competitive global market with increasing awareness on environmental issues, chemical production is making its way toward a paradigm shift to more efficient and more environmentally friendly manufacturing processes. In the pharmaceutical industry, where some remaining challenges still need to be addressed for small molecules APIs manufacturing, scientific advances in organic chemistry offer opportunities to drive a green-by-design approach. From a process chemist’s point of view sustainability entails the development of more efficient, effective and safer reactions. Across many industrial applications, chemical engineers and chemists have the opportunities to address today’s most important problems by innovating from the molecular to manufacturing scales.
After an introduction on the context and challenges for delivering more sustainable APIs process manufacturing, we will review some key technologies that are already demonstrating the environmental footprint reduction. To provide a practical understanding, we will present three case studies illustrating the elaboration of process strategies—from route synthesis to industrial scale—with the ultimate goal of delivering comprehensive and sustainable process solutions.
> Discover the full article on Specialty Chemical Magazine <
Introduction
The pharmaceutical industry is devoting its efforts to develop more sustainable chemistry for modern drug manufacturing and optimizing the synthesis of many pharmaceuticals in terms of greenness. In medicinal chemistry, focusing on the early processes in drug discovery with the goal to reach fast and effective production of promising drug candidates, most laboratories are still employing older, conventional methodologies for the synthesis of their target compounds. Nevertheless, the eco-friendliness of the process is becoming a true key driver. Replacing older methods with benign alternatives are a tremendous opportunity to innovate in some synthetic methodologies and practices.
In 2008, the pharmaceutical company Pfizer developed the first Reagent Selection Guide, as a pioneer in advancements in green and sustainable chemistry. In addition, other pharmaceutical companies such as GSK, Sanofi and AstraZeneca outlined Solvent Selection Guides as tools for making the best choice towards greener and more sustainable chemistry, ranking the most used solvents in terms of their greenness. These guidelines provide an essential educative tool for newcomers in the field.
Aligning sustainability with process intensification (PI).
Process intensification provides the potential to reduce waste, improve energy efficiency, and potentially access new feedstocks.
Currently the fine chemical and pharmaceutical industries are mainly dominated by batch processing, operating in flexible multipurpose batch plants using several consecutive and segmented unit operations/processes both for API (Active Pharmaceutical Ingredient) and formulated drug products.
With increased cost-pressures, industries are looking at opportunities to lower operating costs. As a result, there has been an increasing interest in developing continuous production processes instead of the traditional batch processes.
Continuous processing (CP) offers many advantages including higher product throughput and yield, easier scaling up, more consistent product quality, safer operation under extreme conditions. A CP approach is constrained only by the limits of chemistry and physics, whereas batch processing is often constrained by equipment limits.
From a green engineering perspective, continuous processes can significantly reduce the process mass intensity (PMI) metric. Typically, the separation steps across a pharmaceutical synthesis will significantly contribute to the process mass intensity of a synthesis. Moreover, in terms of energy use, distillation and drying steps alone often can significantly consume the energy requirements of a process.
Typically, flow chemistry enables an increase in mass- and heat-transfer processes, avoiding temperature gradients, heat-accumulation, or temperature hotspots, which can cause a loss in reaction selectivity. This is also actionable for highly exothermic reactions.
Revisiting synthetic methods for environmental benign impact
Making the right decisions regarding chemical processes can be driven through strategic design of synthetic routes and selecting wisely the reagents. Some of the major pharmaceutical and biotech companies, including AstraZeneca, Bristol-Myers Squibb, Eli Lilly, Merck, Novartis, Pfizer, and Roche, created a dataset based on scaled-up reactions. This database[v] contains almost two thousand reactions, to help chemists to choose the most favorable retrosynthetic pathways for product manufacturing.
A crucial metric in assessing and benchmarking progress toward more sustainable manufacturing is Process Mass Intensity (PMI). This metric quantifies process input mass (eg. solvent, water, reagents) per mass of output produced. Typically, solvents and water are the largest contributions to mass intensity.
By using a PMI prediction calculator based on historical information and virtually screening through the database and predictive data, this can help to discriminate among the most efficient and plausible greener routes. Moreover, PMI calculation can provide a useful comparison between different reactions and optimize a proposed synthetic step, always considering the waste management strategies.
Towards greener reactions
Progressing towards more sustainable reactions requires the development of environmentally friendly synthetic routes for both starting materials and APIs. Valuable strategies in this effort include one-pot synthesis and multicomponent reactions (MCRs), particularly effective when utilizing multiple substrates simultaneously or sequentially in the chemical reaction. These approaches play a crucial role in minimizing intermediate purification challenges, resulting in high atom economy and significant waste reduction. Furthermore, the adoption of catalytic processes emerges as a promising alternative, contributing substantially to waste reduction throughout the reaction.
To minimize the use of external energy within a synthesis strategy, unconventional, innovative energy delivery, such as microwave irradiation, sono- and photochemistry are being developed.
While photochemistry has a long-standing history, its traditional reliance on energy-intensive UV light, requiring specific equipment, has encountered challenges related to poor functional group tolerance. However, a contemporary shift is underway towards utilizing abundant and chemically inert visible light, even extending to infrared (IR), representing a significant breakthrough in the field. Unlike thermal activation, the rapid absorption of radiation energy elevates the acceptor to a higher energy level, demonstrating tremendous potential. In medicinal chemistry, photochemistry finds frequent application in catalytic challenges and is widely integrated with flow chemistry.
Typically, the use of protection groups in the synthetic route usually requires additional solvents, other auxiliaries, and an increase in the number of reaction steps, unless using strategies that improve the chemoselectivity of a reaction. This can be achieved through technologies including flow chemistry, click chemistry, biocatalysis.
Enzymatic chemistry employs nature’s catalyst, i.e., enzymes, in chemical processes, represents a highly attractive field in green chemistry. Biocatalysts have many benefits over their chemical counterparts, given that they are compatible with mild reaction conditions such as ambient pressure and temperature, and can become compatible with a growing number of solvents.
Another advantage of enzymes is their chemo-, regio- and stereoselectivities for specific substrates, without any need for additional derivatization, protection, and deprotection steps.
> Discover the full article on Specialty Chemical Magazine <