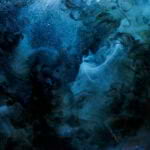
Multipurpose Flow Chemistry
Key advantages of Flow Chemistry
Safety
In Flow conditions, higher exchange surface to volume ratio and smaller volume allow to perform reactions safely compared to batch
- X 200 exchange surface to volume ratio vs batch
- Conditions precisely controlled
- Lower risk of adverse events
- In situ synthesis of hazardous intermediates
Competitiveness
Flow chemistry allows safety and competitive economics for the reshoring of processes previously only performed in Asia:
- Faster reactions: hours to minutes
- Less idle time versus batch processes
- Possibly no intermediate purification step
The initial development time is reduced, and upscaling facilitates compared to batch chemistry.
Flow Chemistry requires lower investment for incremental capacity increase and lower OPEX. Flexible production of required quantities without limitations by batch size.
Possible Intellectual Property generation with new synthesis pathways or conditions distinct from batch.
Improved environmental footprint
Significant reduction of environmental footprint compared to batch:
- ~30% Energy consumption reduction
- FROM 50% TO 80% reduction of solvent consumption
- ~50% Reduction of environmental footprint
Lower need of solvent for mixing and calorific transfer as volume is lower with a high surface exchange.
Possibly no need of (solvent-consuming) intermediate purification step.
Homothetic equipment between laboratory scale and manufacturing scale
From Lab
- Laboratory equipment for fast conditions screening then homothetic implementation for the upscaling to manufacturing scale
- Capacity: 60g/h (non GMP)
To Manufacturing
- GMP Manufacturing at ton scale (50Kg/day – 2 temperature zones)
- Process Analytical Technology (PAT) tools coupled with Chemometrics competencies
- Continuous work-up (2 cascaded mixer-settlers)
Nitration
- Corrosive and hazardous reagent: HNO3
- Risk of overnitration
- Explosiveness of nitrated byproducts
Nitration can be combined with hydrogenation to obtain amines.
Fluorination
- Hazardous reagents: F2(gaseous), HF
- Risk of oxidation side reaction
Possibility to redesign synthesis pathways with late-stage fluorination
Chlorination
- Explosive nature of Cl² with organic volatiles
- Highly exothermic reaction
- Risk of over chlorination
Flow chemistry allows to mitigate several risks associated with batch reactions
Hazardous reagents
- Cyanation: possibility to strictly control HCN through neutralization at the end of the reaction
- Reaction steps using hydrazine
Unstable intermediates
- Oxidation: in-situ formation of unstable Caro’s acid
- Diazotization: possibility to produce in situ the unstable diazonium intermediate then perform the next step
Reaction conditions
- Hydrogenation: H² pressure management
Ability to perform reactions above solvents boiling point
Case study: safe and selective dinitration
Over the last 20 years, the industrialization of such reactions has become rare in Europe. Industrial plants have some difficulties of maintaining their implementation in an acceptable environmental and safety conditions with regards to local regulations. In fact, a large part of the production of APIs has been exported to Asia. A crisis such as the Covid-19 is a clear indication of the fragility of the drug supply chain in western geographical areas.
SEQENS is investing in Flow chemistry technology to improve competitiveness and safety for custom synthesis.
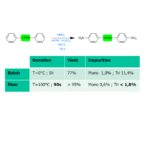